Completed: December 2022
While working at the Mechanical Undergraduate Laboratory at my university, two of my tasks was to develop a workflow for reverse engineering objects using 3d scanning and also to create a series of trophies using turbine blade, as seen below:
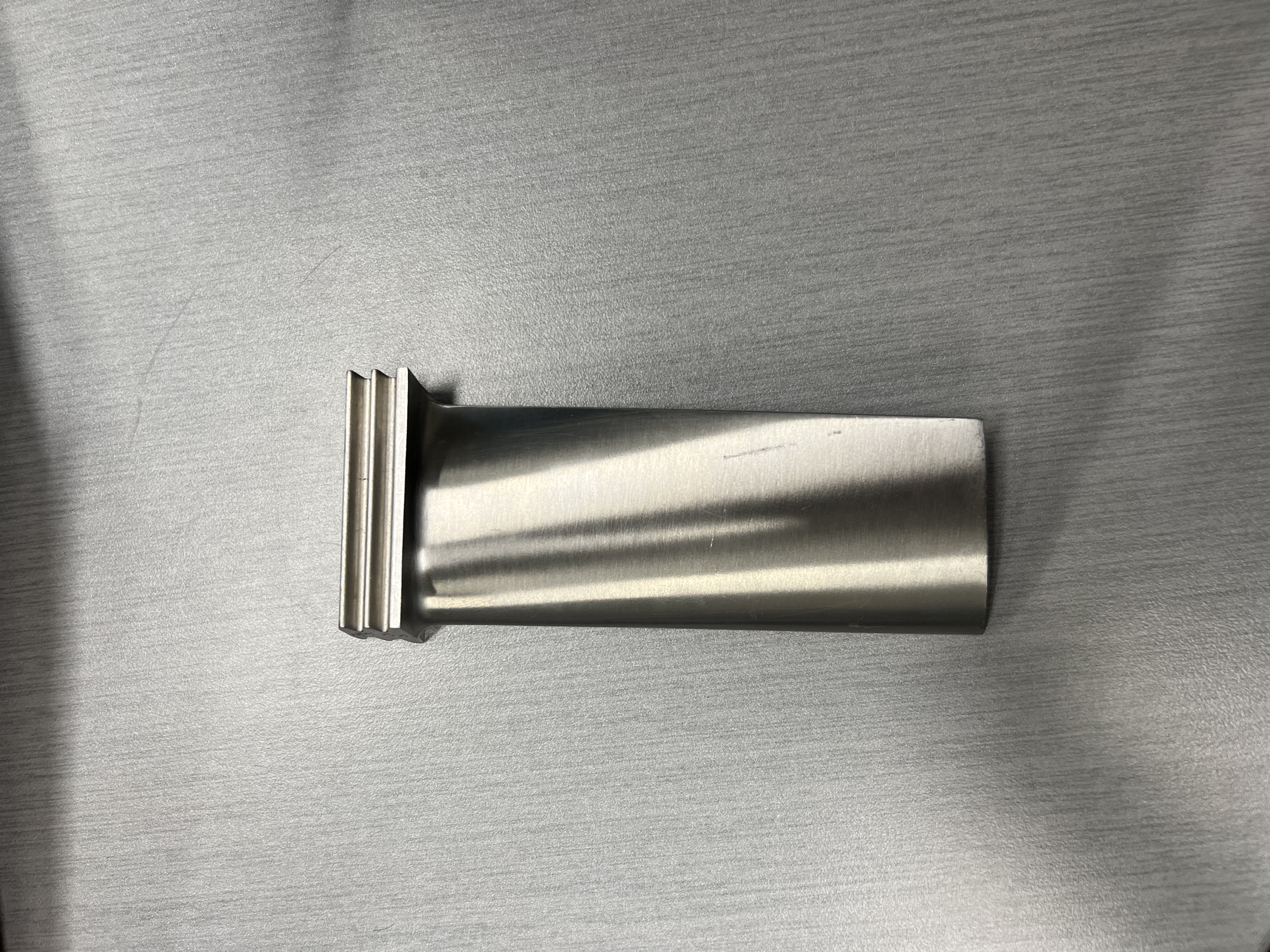
A test of the trophy was made by clamping a blade to a plate on the mill. This was inefficient for many reasons.
- The blades have a irregular shape so its hard to mount to using clamps
- Everytime a new blade would be processed, the references on the mill would have to be determined again.
My coworker suggested that since we have the 3d scanners and its something I’m already working on, why not reverse engineer a model of the blade and then 3d print a mold that can be used to secure to blade on the mill. As luck would have it, he also found a video by Making for Motorsports doing exactly that. It was released a couple days before our conservation so it was quite the coincidence. The video explained how to use Fusion 360 to make a model from a mesh.
So that’s what we did. We took a scan of the blade using a Roland LPX-600, imported it into Fusion and then made a model of the blade.
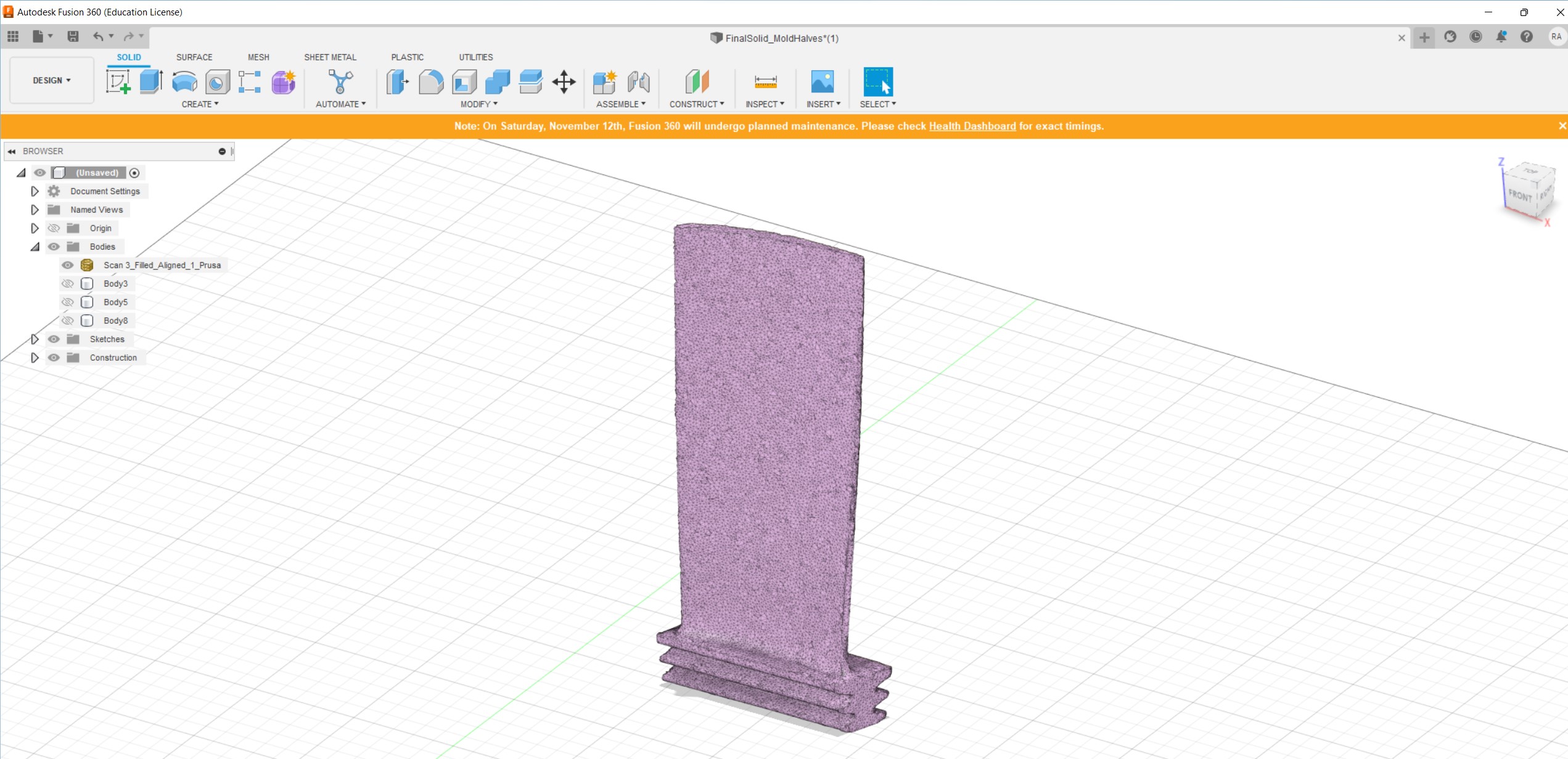

With the model made, we made a mold that would be used a jig for the blades. See the images of the model below.
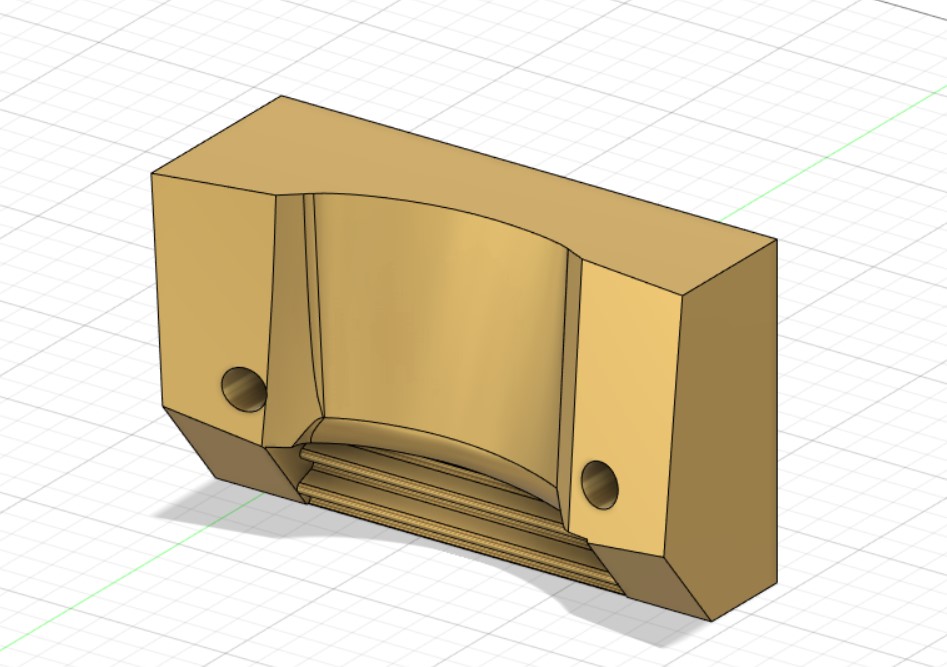
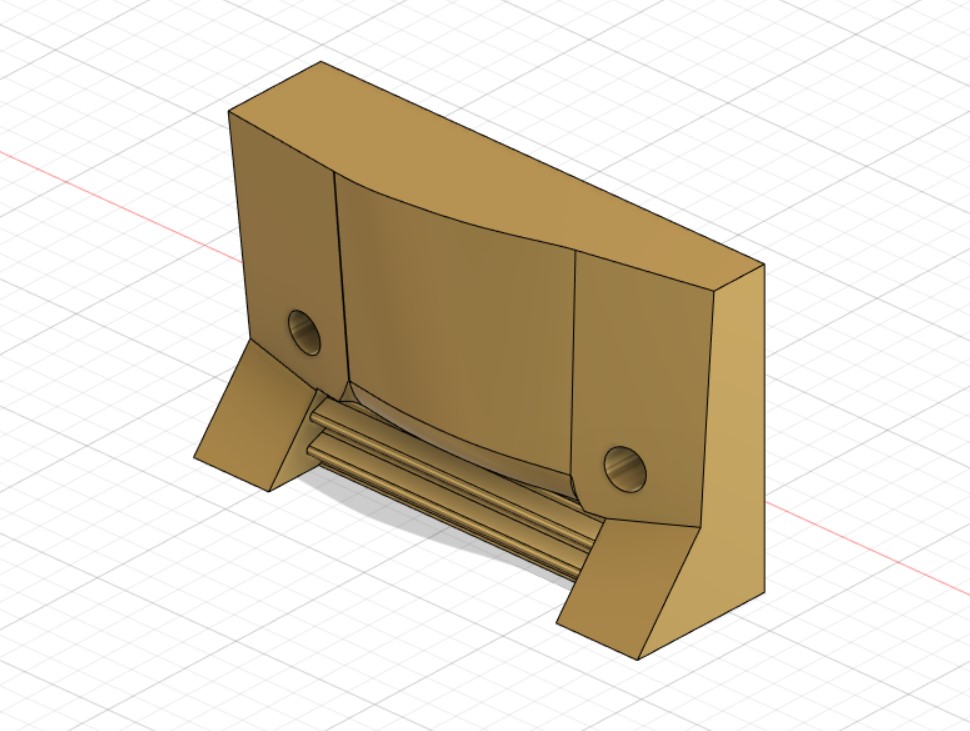
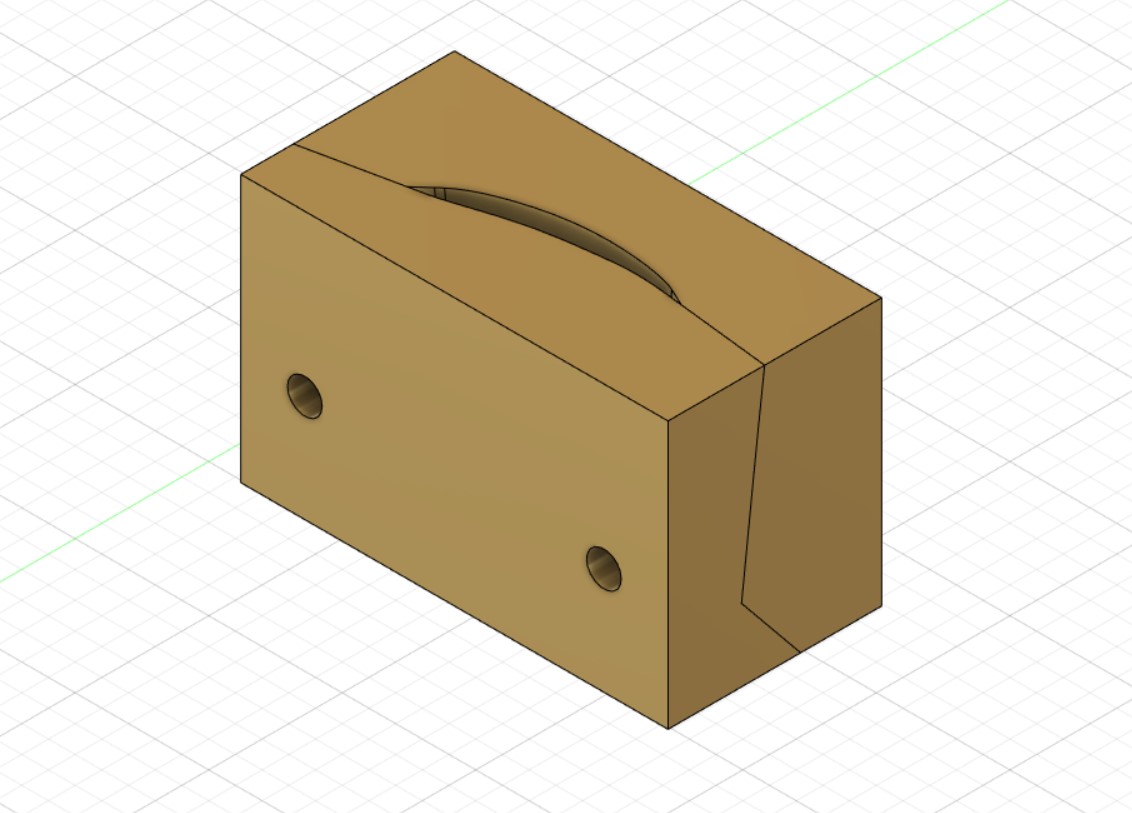
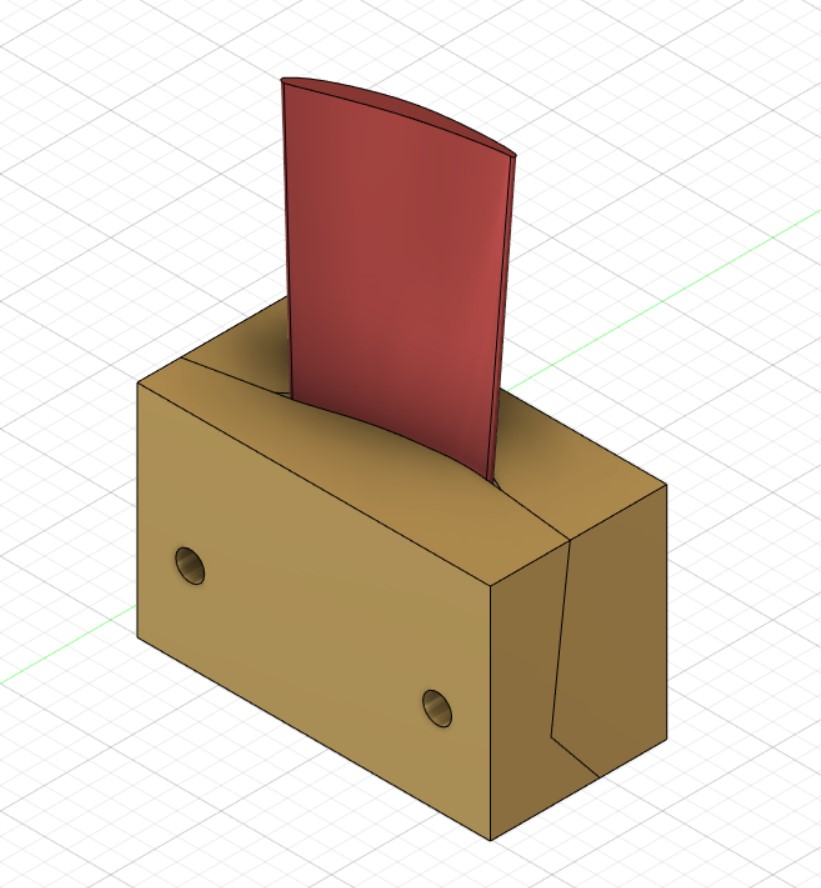
The completion of the mold, marks the end of the 3D scanning/reverse engineering portion of the project. Next was to finish fabricating the trophies.
First, I used an aluminum plate as the base to secure the jig to. I used an end mill to square two of sides of the plate. Then I drilled, countersunk and tapped holes that would be used to fasten the jig to the plate.
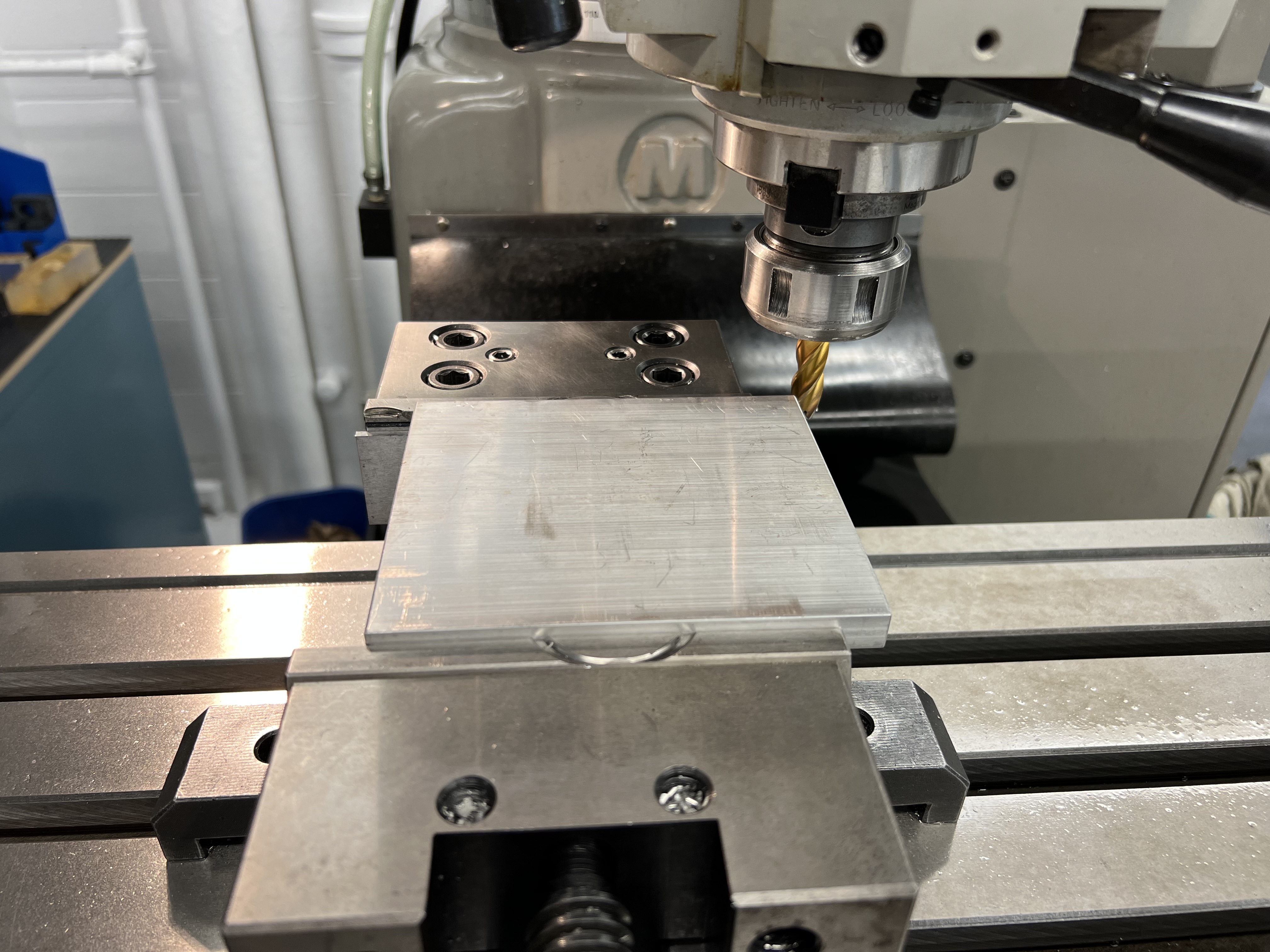
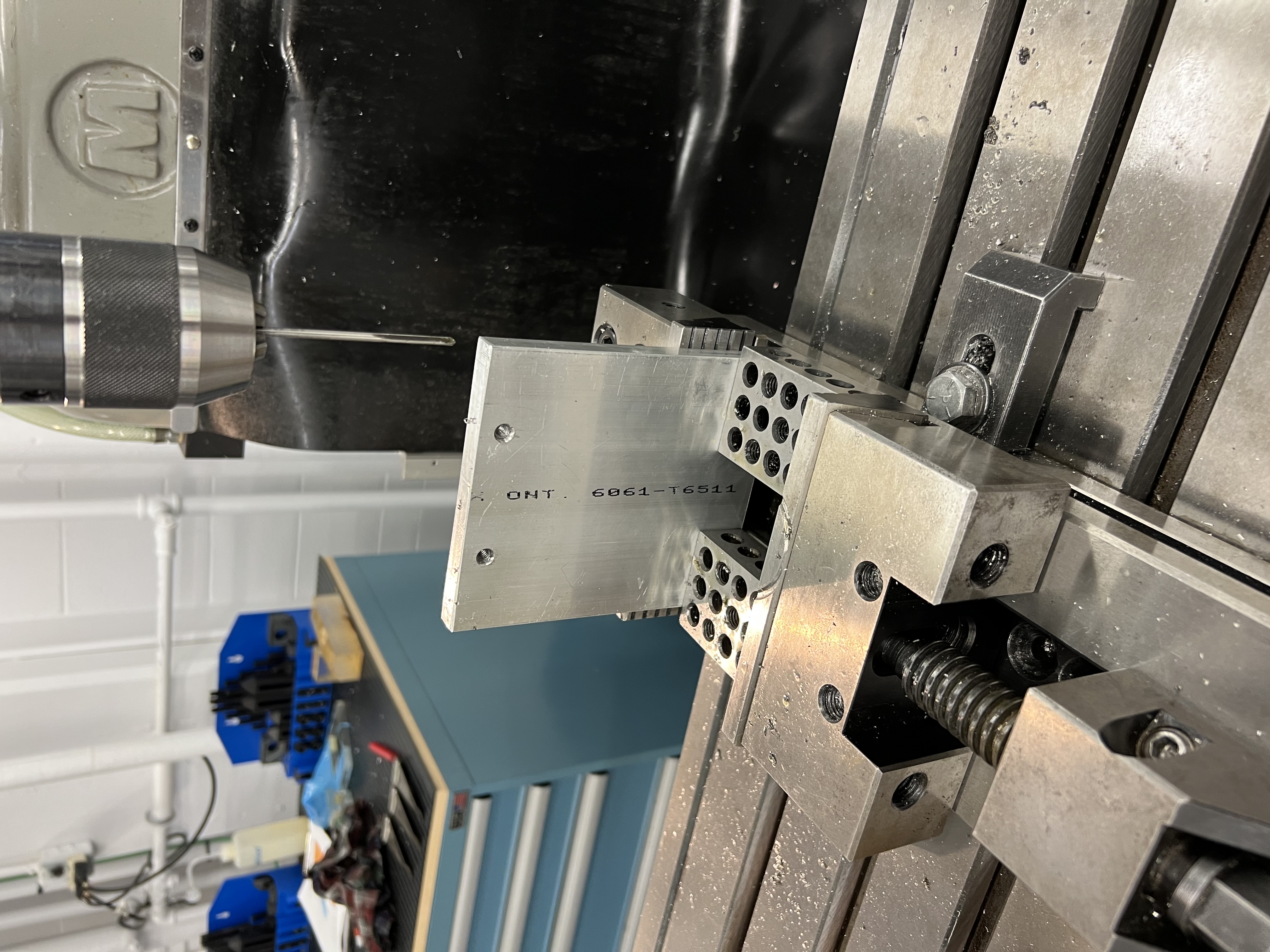
Once the plate was complete, it was secure to the mill, and the operations for the blades could begin. The jig with the blade assembled can be seen in the picture below. I used an edge finder to get the center the blades and then drilled and reamed holes to fit the dowel pins. This was rinsed and repeat for 10 blades. The jig worked really well, but its not perfect. If I was going to improve it, I would design the mold so that half would stay permanently fixed to the plate and then the other half would be removed to swap the blades. This would ensure that the jig didn’t move during swaps.
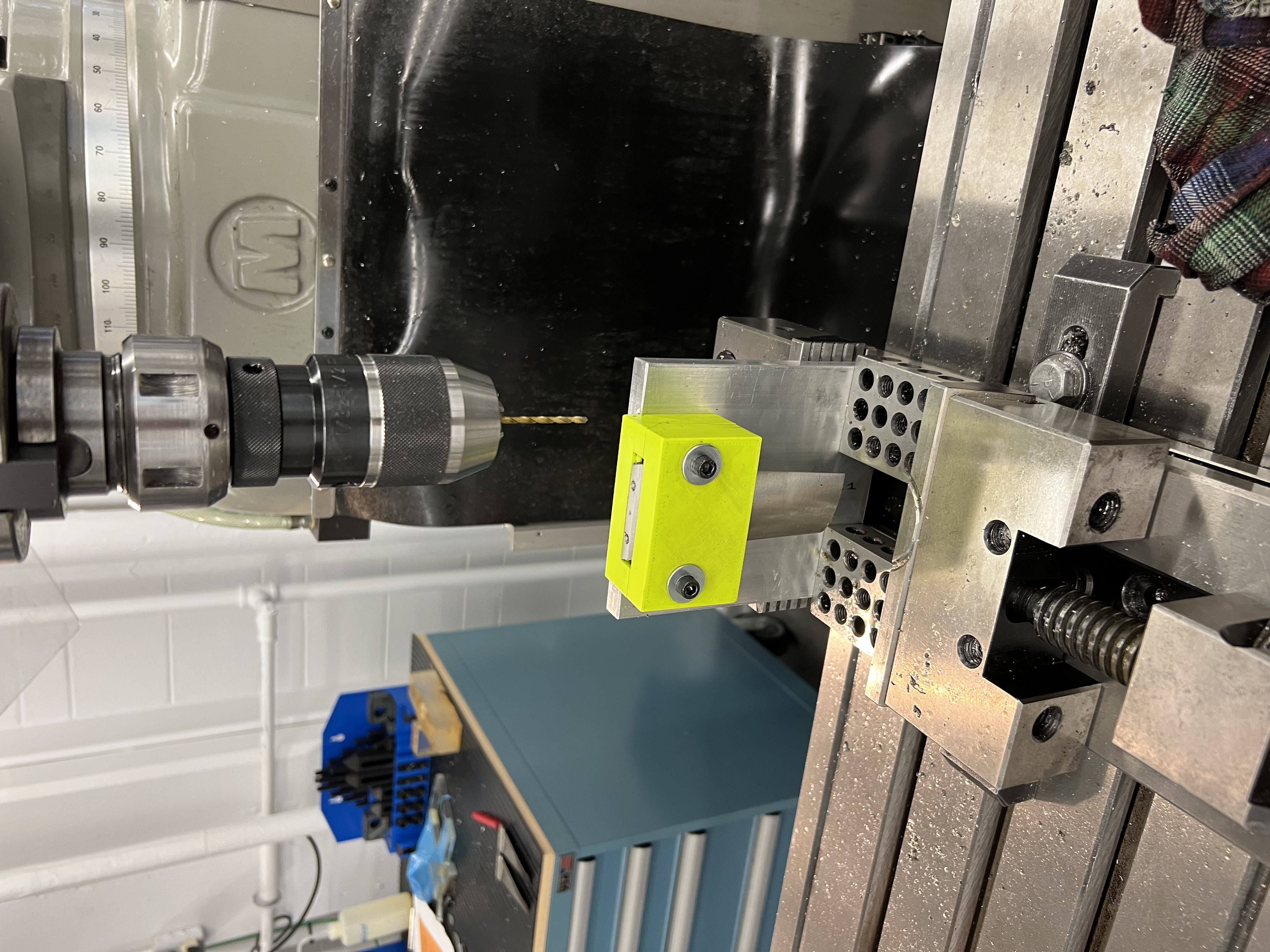
Once all the blades were completed, the wooden bases for the trophies had the equavilent holes drilled and reamed into them. The bases were finished with a Polyeurothane coating. Using the dowel pins, the blades were secured to the bases.
Nameplates were made for the trophies by laser marking some stainless steel rectangles. The laser marking spray was created by CerMark and basically, you spray this “paint” over the metal piece and when you engrave over the plate, the heat bonds the paint to the plate.
The finished result looks like this!
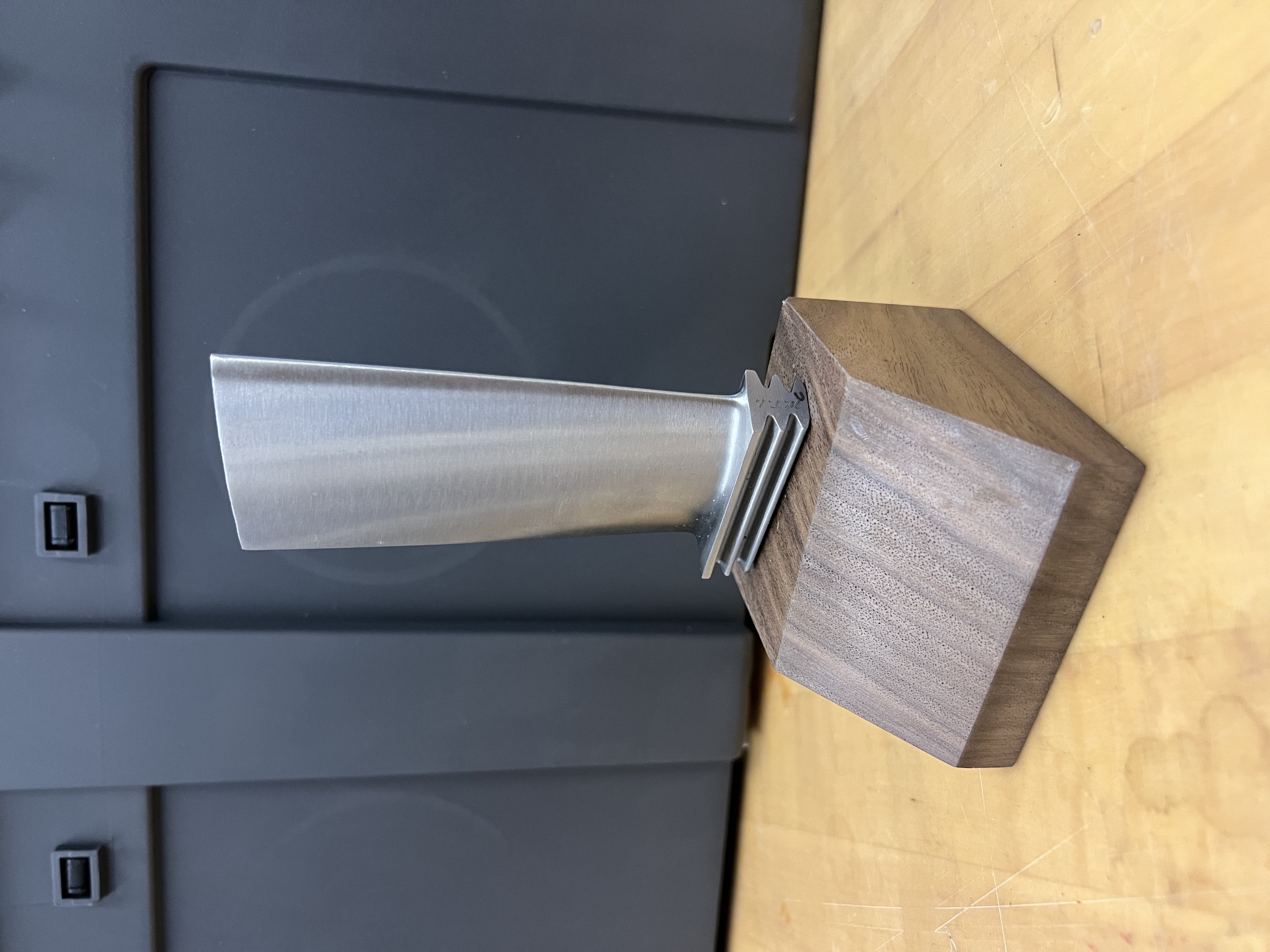